

It is shown that with an optimal system the transmitted forces may be reduced significantly particularly when orientation angles are also treated as design variables. Meanwhile, the mounts have to be stiff enough not to allow the engine deflection to exceed its limits under static and low frequency loadings. The objective is to select the stiffness coefficients and orientation angles of the individual mounts in order to minimize the transmitted forces from the engine to the nacelle. The mounts are modeled as three-dimensional springs with hysteresis damping. The base (nacelle) is modeled with mass and stiffness matrices and structural damping using finite element modeling. The engine is modeled as a rigid body connected to a flexible base representing the nacelle. The proposed method is a simple and efficient practical approach to achieve improved performance using the fewest number ofĭesign optimization of aircraft engine-mount systems for vibration isolation is presented. The results show that the performance of control system with 5 andĮven 3 optimally placed sensors is at least 8% better than the original benchmark building design with 5 sensors. The benchmark building for placement of 5 and 3 sensors. The efficiency of proposed method is evaluated on To new or existing buildings, as the accelerometer placement is trivial. Due to low cost, high reliability, controlĮffectiveness as well as installation simplicity, acceleration type sensors are considered.
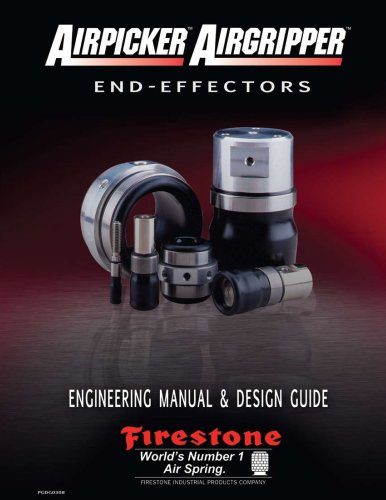
Not depend on the control strategy and nonlinear dynamics of the control system. The optimal placement scheme is general for passive, active and semi-active controls and it does In this paper, a general method based on a proposed constrained GA is suggested to optimally These experimental results show a 7 to 46 times improvement in vibration isolation from the baseline configuration.Īppropriate sensor placement can strongly influence the control performance of structures. Finally, a number of optimized designs obtained from the GA searches are tested in the laboratory and compared to the baseline design. Results show that this approach leads to either infeasible or poor designs. An alternate approach is also tested on this problem: it uses continuous optimization, followed by rounding of the solution to neighboring discrete configurations. However, the GA runs provide a variety of optimized designs with predicted performance from 30 to 70 times better than a baseline configuration.
#Firestone airmount catalog series#
A series of GA runs reveal difficulties in the search on this heavily constrained, multimodal, discrete problem.
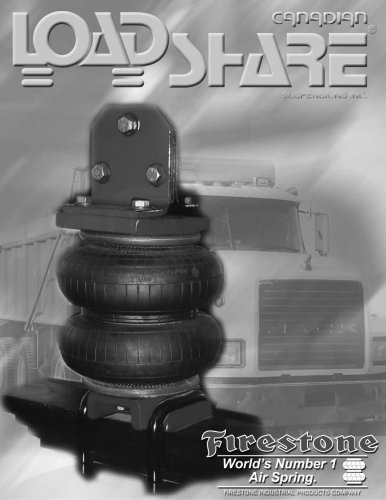
Design constraints dictated by hardware and experimental limitations are implemented through penalty function techniques. The system is modeled in MATLAB and coupled with the GA available in the DAKOTA optimization toolkit under development at Sandia National Laboratories.

Because the available locations for the isolators are discrete in this application, a Genetic Algorithm (GA) is used as the optimization method. The study uses isolators with fixed properties and evaluates potential improvements to the isolation system that can be achieved by optimizing isolator locations. An analytical and experimental study is conducted to investigate the effect of isolator locations on the effectiveness of vibration isolation systems.
